Having an accurate understanding of your business costs is incredibly important in creating a profitable and successful endeavor. To that end, the choice between job and process costing is a very important choice indeed, and understanding the differences between the choices will allow you to make a reliable and informed decision about which option will best suit your business. Depending on what industry you are in and how you are operating, you will likely find one or the other to be a more suitable option for all of your costing purposes. Unless you offer a variety of both customised and standardized products, you are unlikely to need to use both types of costing processes.
Job Costing
Imagine, if you will, that you are a skilled artist, taking commission for various requests for custom pieces. Each product you create will inevitably use different quantities of material, take a variety of time lengths to complete (for which you might use a time keeping app), and generally cost differing amounts depending on the order you receive.
This is job costing: calculating your costs on a case by case basis, because what you are doing is not the same every time you need to appraise your costs on a job by job basis rather than relying on a homogenised standard cost for each item you produce or service you provide. If you are providing a homogenised service, it almost certainly will not be for you – why calculate cost on a job by job basis when every case uses the same resources?
Whether job costing is right or not for your business may well depend on your industry – for a builder, every project is unique, but when it comes to producing pens, the resource requirement for each will be exactly the same and so job costing will be unnecessary.
How to Calculate Job Costing
Let’s take a look at how you might break down your job costing calculations in a very simple/basic way.
Calculate Labour Costs
This is the man hours you will have committed to the project – you have to pay your worker’s salary or wages. The wages you pay specifically for the time worked on the project can then be added to the cost of the project.
Calculate Material Costs
Depending on the industry you are in, there will be a variety of materials which are important in completing your work effectively. Some things are obvious, for example the construction materials required for a building project, or physical supplies needed to carry out your design project. Even stationary items could be considered material costs relevant to the project they are needed for.
Estimate Applied Overhead
Your Applied overhead costs include any cost that cannot be directly assigned to a cost object, such as rent, administrative staff compensation, and insurance. But these costs are not directly a part of the costs explicit only to this project – they are costs relevant to the general operation of the business rather than one job. So, you will need to estimate just how much of these overhead costs need to be applied to this project in particular.
Process Costing
In stark contrast, process order costing is something to be used when your product is not customised but rather is uniform, where the costs for each production will be the same, using the same amount of resources each time without any variance from job to job. Process costing takes each stage of manufacturing (each process) and costs for that entire process over the time period being looked at on the understanding that each individual unit being produced will take an identical quantity of each ‘process’ to produce.
Examples of processes might be the cost of packaging goods, of raw materials going into production, or of assembly. Because the cost per unit for each process is the same, the costs can be collated into these process costs over a given time period/production quantity, allowing for easier management of larger scale costs as compared to job costing, as identifying a cost per unit is possible in process costing only when we know for certain that each unit has an identical cost.
Ultimately, job order costing and process costing are cost accounting systems which are both viable – the key is to identify unique circumstances and needs of your business.
How to Calculate Process Costing?
There are a few different types of process costing which can be used depending on your situation. You can use weighted average costs, in which you work out an average cost per unit across your offerings. Calculating standard costs is somewhat similar – the main difference is that you would assign a standard cost when calculating your averages, rather than using the actual costs. A final consideration is the FIFO system – if you are dealing with a goods oriented manufacturing or sales industry, you are likely already familiar with the idea of ‘first in, first out’. Using this method can help to reduce the chances of your stock becoming obsolete as you ensure that the oldest units of stock are being sold first. But it can be hard to implement and a little more complicated that just working outa weighted or standard average cost per unit and applying that.
So, What’s the Difference Between Job Costing and Process Costing?
It’s pretty easy to pick out the key differences between the job costing and process costing systems from the sections we’ve provided explaining each one, but it is always helpful to have a more visual way of differentiating between different concepts, so let's write up a table showing the key differences between each.
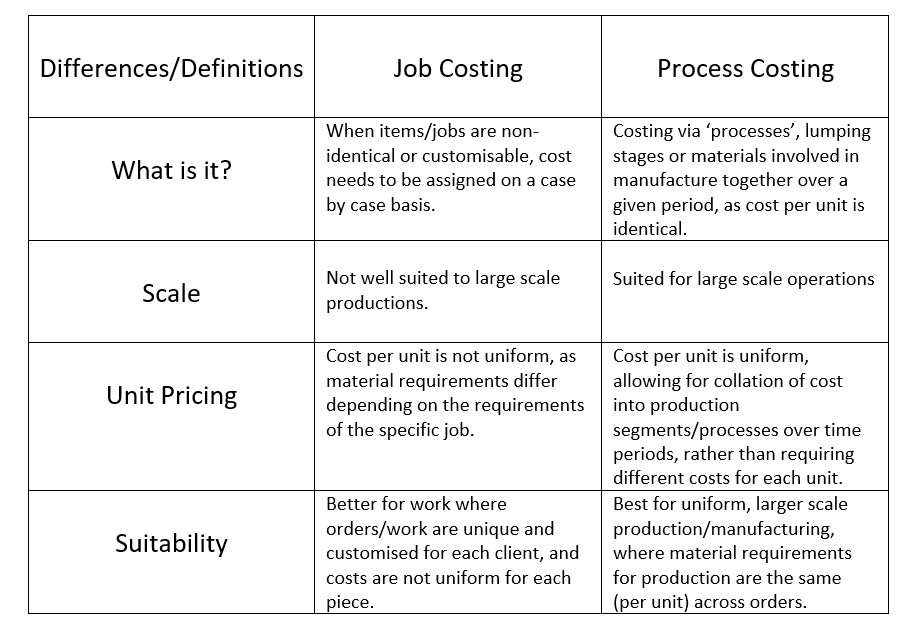
Which Companies Use Process Costing and Which Use Job Costing?
You may find that the case for your business is clear cut, and that one or the other of job/process costing is clearly the superior choice for you. Or you might be in a situation where some mixing and matching is required, if you are dealing in both uniform products and more customisable, unique orders. Some industries will have a clear leaning towards one, some will be more balanced.
In the end, the choice of which to use is one which should be made based not on industry or on what your competitors/colleagues are doing, but on the unique requirements of your business. What will work best for you is something only you can know.